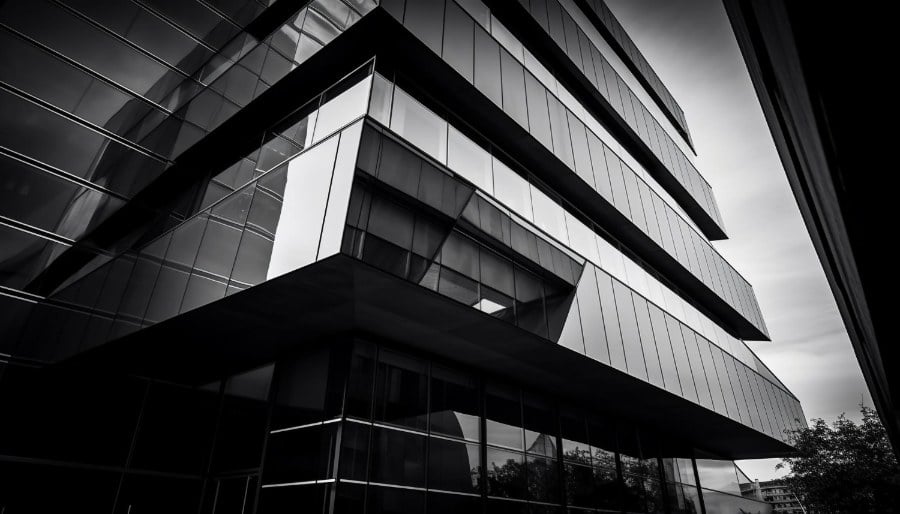
The way we build now…emerging technologies are transforming modern construction
It’s hard to imagine any building as a paradigm for emerging technology: after all, apart from a few doors and windows, buildings have so few moving parts, and unlike computers and satellites, they’re rooted firmly to the earth. So, you might also be pushed to think of a less likely candidate for fast-track status in these rapidly evolving, high-tech times…But if so, you need to dig a little deeper. All those brick-clad houses and office blocks, hospitals and schools on the high street…they might look pretty much as they always did (from the outside, at least), but over the last decade or so (and getting faster track every day), how they’re being built has been transformed by nothing short of a technological revolution.
That humble old building, seemingly so traditional and trenched deep in the ground, is now just as much a miracle of our modern times as ChatGPT, Blockchain, and FinTech. This makes this an especially good time to take a closer look at how we build and live now…
Breaking out of the box
In the not-so-distant past (and occasionally even now), most buildings began their life on a drawing board, and the designer (or architect, assuming there was one) would periodically visit the land slated for development, literally to check the lie of the land. And then, eventually, on a timeline that made your average London to Manchester train look like Usain Bolt, a set of plans would be produced (four feet wide by three deep…so hardly pocket-sized). The surveyors and engineers on site would begin to find disturbing variances between the blanket-sized plans and the actual topography of the site. That’s because the people producing the projects had been working in an office somewhere, with very little understanding of what the area looked like or what the building would look like when it finally took shape.
Mismatches of that kind often meant walls had to be removed (to make way for reality), and drainage systems dug up because the fall didn’t quite match what had looked like reality back in the office. The list of gruesome disconnects went depressingly on…which was one reason cost overruns, material wastage, and unscheduled delays were so much a feature of dinosaur construction back in the bad old days.
Happily, that’s all changing.
Building Information Modelling…and so much more
Building Information Modelling (or BIM) uses digital technologies to create a 3D model of the building, as well as its related components, which enables architects, engineers, and contractors to collaborate much more efficiently from the outset, significantly reducing error rates and radically reducing levels of waste (bear in mind that traditional construction has historically been the biggest producer of industrial waste in the world). And BIM also allows productivity rates, sustainability levels, and overall quality assurance standards to go up, too…which is why, for the last decade, it has become a must-have technology for any construction project. And, if nothing else, it’s nice finally to ditch those blanket-sized plans…modern construction professionals are working from a laptop, tablet, or mobile phone and doing much better.
3D Printing Technologies also facilitate the creation of much more accurate large-scale modelling (using a layer-by-layer approach). The scope for increased accuracy makes it possible to create complex materials on site (from scratch), again reducing costs (see above) and maximising the bottom line by dispensing with redundant transportation and storage costs. The tallest 3D-printed residential building in the world (three stories high) was recently completed in Wallhausen, Germany,(www.stirworld.com): and all the materials were bespoke and created on-site, with no individual parts that required shipment or separate assembly.
And that’s by no means all...
Other emerging technologies, such as Advanced Robotics, AI, Augmented Reality, Blockchain, and, inevitably, the Internet of Things, are also increasingly combining to improve site efficiencies and (not unimportantly) site safety standards. Drones are being used to conduct more accurate surveys than ever before, in addition to enabling buildings under construction to be inspected from angles previously the stuff of science fiction.
Modular Construction
And then, of course, when it comes to advanced building technologies, Modular Construction is a class of its own: creating units and components in carefully controlled conditions (no more wading around in the mud), which can then be readily assembled on-site, at a third of the cost of traditional construction, and twice as quickly as well. That means more buildings where we need most (especially more new homes in these challenging times).
If ever there was a paradigm of what emerging technologies can achieve, Modular Construction is it.
Executive Overview
I expect we’ve all been troubled by the emerging RAAC crisis in Britain’s Schools…but the answer’s staring us in the face: Modular Construction.