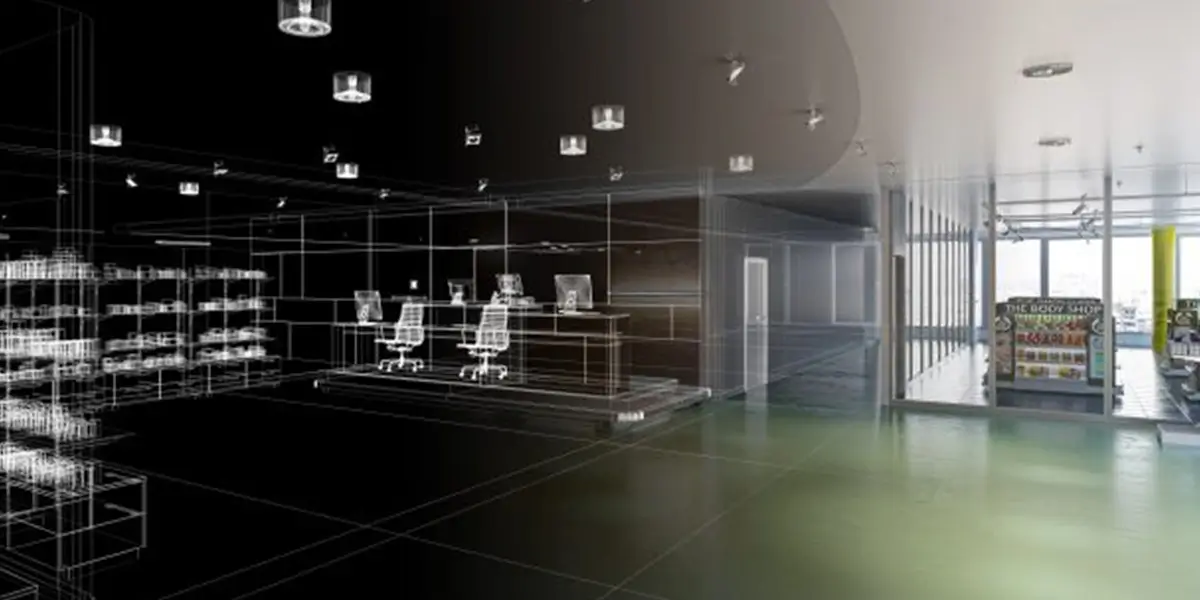
Defeating COVID with Pace and Conviction…Major New Hospitals are part of the story
Health Authorities across the globe have been increasingly turning to Modular Construction as part of the fight against COVID 19, and the NHS Nightingale Hospital in East London, a 4000-bed facility with capacity for 16,000 medical staff, was a prime example: developed from concept to completion in less than nine days, which is just the sort of pace, focus and conviction that we need to meet and defeat challenges posed by the pandemic n these unprecedented times.
And in Wuhan, the pandemic’s ground zero, two major hospitals were built from scratch in less than two weeks using state of the art modular technologies. Like the Nightingale in London, the City’s 1000 bed Huoshenshan Hospital was completed in nine days, with all of its key components being prefabricated off-site and assembled to plan on location: covering 60,000 square meters, the new hospital spans two floors and has thirty critical care units and quarantine wards. Its sister facility at Leishenshan was built on an equally impressive scale and finally topped out in just seven days.
But none of that is especially surprising, given Chinese Authorities have been here before and know exactly what they’re doing: Beijing’s colossal Xiaotangshan Hospital was built at breakneck speed in 2003 to confront (successfully) the burgeoning SARS crisis. The entire hospital was completed in seven days using modular construction techniques, where traditional technologies might have taken anything up to two years, but the epidemic wasn’t offering any quarter in 2003, and it’s no different now…
In fact, it’s precisely this unforgiving dynamic of extreme time pressures meeting unprecedented demand for public safety that has made Modular Construction so important at the moment. One of the recent hospital projects in Wuhan used re-targeted components from more than 3000 flatpack housing kits, modified by size and materials to meet the exacting requirements of a modern healthcare facility. You simply can’t do that with a conventional inventory of precast concrete blocks, steel girders and bricks: in addition to which Modular Construction has also shown itself particularly adaptable in matching the demands of modern clinical projects, with optimal outcomes on both hygienic environments and clinical delivery platforms.
For example, those new hospitals in Wuhan needed thicker internal walls than usual to prevent the virus from spreading from individual isolation units: something which was easily accomplished at a stage when the units were still being modified and constructed off site under controlled conditions. Specialist devices and medical equipment were supplied by external contractors and added to the building’s structure before final assembly: everything from oxygenation systems, aspiration units and surgical scrub facilities. And Modular Construction also needs far fewer labourers working at the final assembly site, working for far shorter periods (a lesson graphically illustrated at the Nightingale in London) each of which significantly reduces the risk of a virus spreading during assembly. Social distancing is built into the process.
And let’s not forget that there are significant benefits for the future as well: unlike a conventional hospital, anchored in steel and concrete, a modular project can be dismantled, removed by truck and recycled when (happily soon) it is no longer needed to fight off the pandemic. The steel core can also be recycled and sold back to the original suppliers…there’s a world waiting for us after COVID 19 has finally been defeated, and we need to look after that too.
Modulex Construction is the World’s largest and India’s first Steel Modular Building Company. It was established by Red Ribbon to harness the full potential of these fast-evolving technologies and deliver at a pace to meet the evolving needs of the community.
Executive Overview
Over recent weeks we have seen a significant increase in enquiries for Modulex to become involved in the creation of new triage units, testing facilities, emergency areas and isolation wards so as to meet the immediate challenges of the pandemic. And over the longer term we are looking too at producing ICU Rooms and related Care Facilities as well as permanent ICU Patient Facilities and Non-Critical Care Units.
I’m extremely proud of the part Red Ribbon and Modulex are playing.