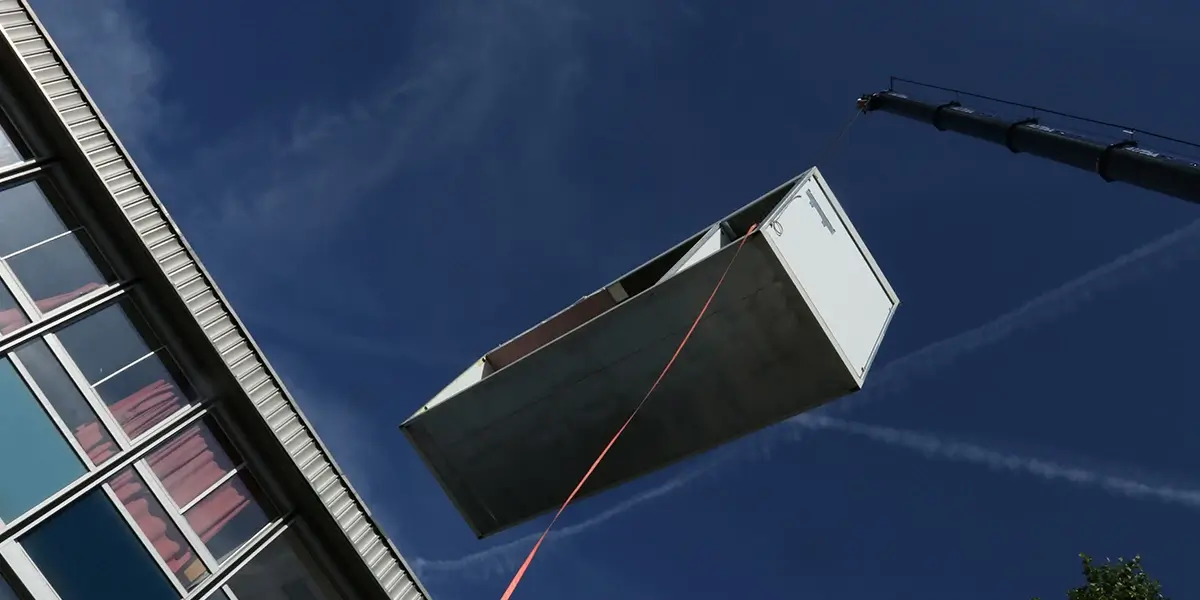
Planning for the Future... New World Logistics and Modular Construction
Stick Build Construction is today’s wattle and daub: the future belongs to Modular Construction, creating components in controlled conditions and delivering them on site in a third of the time, and a third the cost of outdated technologies. So lets be clear what we mean by “Stick Build” here, we mean those dinosaur supply chains that send off endless truckloads of bricks, cement and steel: dumping them daily on construction sites across the globe, knee deep in mud for half the year, and looking as though they stepped straight out of the Middle Ages (which, for the most part, they have). And given the current shortage of new homes and infrastructure worldwide, that’s simply not good enough anymore. Modern construction needs modern technologies, and better supply chains…Modern Construction needs Modular Construction.
Construction Delays
The biggest single cause of construction delays, and the principal reason we’re currently facing a worldwide shortage in housing at the same time homelessness has risen to record levels, is the stubborn adherence of dinosaur contractors to historically inefficient technologies. But the key to unlocking those inefficiencies is quite literally staring them in the face: modular manufacturing and assembly, combined with effective inventory management, has the potential to respond proactively to disruptive site variations (rain in particular): optimising decision making and opening the way to make housing aspirations a practical reality.
Moving Forward: a New Way of Building
Traditional construction has always relied too heavily on over extended and cumbersome supply chains: drawing as it does on multiple suppliers who deliver straight to site, and rarely (all too rarely) make use of consolidated distribution centres. And one predictable outcome is that familiar, long line of trucks, choked up in traffic jams and belching their way to inner city locations where most construction works still take place: but you probably know that already, you’ve probably been stuck behind one on your way to work… Added to which Inner City locations have limited storage space, making off site warehousing ever more essential, and introducing yet another link in an already overextended supply chain.
But you can say goodbye to all that with Modular Construction: materials are produced and delivered on site on demand, responding piece by piece to orders placed centrally from the site itself. All of the relevant information, including quantities and timing, can be taken directly from the master construction schedule, which means Modular supply chains are more effective and way…way more straightforward than their conventional counterparts. Any unexpected deviations in the schedule can be ironed out in real time along the way: deliveries of components can be temporarily halted and held back until they’re needed. That’s all made possible because only very rarely do Modular Projects send materials directly to the site: most are transported to the manufacturing facility in the first instance, where they are converted into core products and components.
Which is why recent research also suggests Modular Construction is much less vulnerable to procurement bottlenecks: when production falls short of demand (as it often does on conventional projects), Modular Technology provides a ready buffer against delays, pre-calibrated as it is to match on site demand with a seamlessly structured supply link. In stark contrast to conventional logistics, where some level of inventory always has to be retained as “safety stock”, modular output is meticulously pre-planned to ensure production matches demand at the conclusion of the project. So no more rusting girders left behind after the workers go home, no more piles of unusable broken bricks and off cuts of waste wood: Modular output is not just faster and less expensive, it’s greener too (www.aprao.com).
On site assembly costs are also lower: mostly because operational oversight has been a notoriously unreliable science on traditional projects (to put it mildly): workers retreat with exasperating regularity to their huts whenever it rains, and when its not raining they’re wading through mud, or waiting for the next truck to turn up. Dinosaur Contractors have traditionally seen project delays as inevitable, but they don’t have to be, not anymore: you can’t stop the rain, but you can outsmart it.
That’s what Modular Construction is all about.
Executive Overview
Every day we read reports of the increasing importance Modular Construction has for global housing and infrastructure projects: and I’m not surprised, with radically changing demand patterns it’s going to be a key part of all our futures.